- Relationship Between Wire Gauge and Ampacity
- How Wire Gauge Affects Ampacity
- Ampacity at Different Temperatures
- AWG Wire Gauge Ampacity Chart
- Wire Gauge, Resistance, and Voltage Drop
- Key Characteristics of Battery Cables
- Ampacity of Battery Cables
- Voltage Drop Considerations for Battery Cables
- Choose the Right Battery Cables for Different Applications
- Summary
An In-Depth Guide to Cable Gauge Amps
- Relationship Between Wire Gauge and Ampacity
- How Wire Gauge Affects Ampacity
- Ampacity at Different Temperatures
- AWG Wire Gauge Ampacity Chart
- Wire Gauge, Resistance, and Voltage Drop
- Key Characteristics of Battery Cables
- Ampacity of Battery Cables
- Voltage Drop Considerations for Battery Cables
- Choose the Right Battery Cables for Different Applications
- Summary
‘It’s the little details that are vital. Little things make big things happen.’ by John Wooden
A cable gauge is the measurement of how thick or wide the conductive wires in a cable really are. The American Wire Gauge (AWG) system is used to measure gauges in the United States. It is a standard measure that was made to make sure that everyone in the industry follows it. The AWG number is inversely related to the diameter of the cable. This means that the wire’s diameter is smaller as the gauge number goes up. A 10 AWG cable, for instance, is thicker and can carry more current than a 16 AWG cable. The first in the AWG system is 0000 (or 4/0), which means the cable is very big and can carry a lot of electricity. On the other hand, smaller gauges (30 AWG or greater) are better for electronics and low-current uses. Cable gauge measurements are very important because they determine things like the cable’s ability to carry current (amperage), its electrical resistance, its flexibility, and whether it is generally suitable for a given application.
Other cable gauge systems include:
Metric System: Uses cross-sectional area in square millimeters (mm²) instead of a numerical gauge. For example:
10 AWG ≈ 5.26 mm²
4 AWG ≈ 21.2 mm²
SWG (British System): Similar to AWG but follows a different scale, requiring conversion for accurate selection.
Relationship Between Wire Gauge and Ampacity
Ampacity, the maximum current a conductor can safely carry without exceeding its temperature limit, closely correlates with the cable’s gauge.
How Wire Gauge Affects Ampacity
The thicker the wire, the lower its resistance, allowing it to carry more current (amps) without excessive heating. Choosing an undersized wire can lead to:
verheating.
Voltage drop.
Power inefficiency.
Ampacity at Different Temperatures
A wire’s ampacity depends on the operating temperature and insulation type:
Standard PVC insulation: Max temperature 60°C – 75°C.
XLPE or high-heat insulation: Max temperature 90°C – 125°C.
Higher temperatures require derating, reducing ampacity to prevent overheating.
AWG Wire Gauge Ampacity Chart
AWG | Diameter (mm) | Copper Ampacity (60°C) | Copper Ampacity (75°C) | Copper Ampacity (90°C) | Aluminum Ampacity (60°C) | Aluminum Ampacity (75°C) | Aluminum Ampacity (90°C) |
---|---|---|---|---|---|---|---|
4/0 | 11.684 | 195 | 230 | 260 | 150 | 180 | 205 |
3/0 | 10.404 | 165 | 200 | 225 | 135 | 155 | 175 |
2/0 | 9.266 | 145 | 175 | 195 | 115 | 135 | 155 |
1/0 | 8.252 | 125 | 150 | 170 | 100 | 120 | 135 |
1 | 7.348 | 110 | 130 | 145 | 85 | 100 | 115 |
2 | 6.544 | 95 | 115 | 130 | 75 | 90 | 100 |
3 | 5.827 | 85 | 100 | 115 | 65 | 75 | 85 |
4 | 5.189 | 70 | 85 | 95 | 55 | 65 | 75 |
6 | 4.115 | 55 | 65 | 75 | 40 | 50 | 55 |
8 | 3.264 | 40 | 50 | 55 | 30 | 40 | 45 |
10 | 2.588 | 30 | 35 | 40 | 25 | 30 | 35 |
12 | 2.053 | 20 | 25 | 30 | 20 | 25 | 25 |
14 | 1.628 | 15 | 20 | 25 | 15 | 20 | 20 |
16 | 1.291 | 10 | 13 | 18 | 10 | 13 | 15 |
18 | 1.024 | 7 | 10 | 13 | 7 | 10 | 12 |
20 | 0.812 | 5 | 7 | 9 | 5 | 7 | 8 |
22 | 0.644 | 4 | 5 | 7 | 4 | 5 | 6 |
24 | 0.511 | 3.5 | 4 | 5 | 3.5 | 4 | 5 |
26 | 0.405 | 2.5 | 3 | 4 | 2.5 | 3 | 4 |
28 | 0.321 | 1.8 1.5 | 2.5 | 3 | 1.8 | 2.5 | 3 |
30 | 0.255 | 1.5 | 2 | 2.5 | 1.5 | 2 | 2.5 |
Note:
AWG: American Wire Gauge (the smaller the AWG number, the thicker the wire).
Diameter (mm): Diameter of the wire (in millimeters).
Copper Ampacity (60°C, 75°C, 90°C): Maximum current-carrying capacity of copper wire at different temperatures (in amperes).
Aluminum Ampacity (60°C, 75°C, 90°C): Maximum current-carrying capacity of aluminum wire at different temperatures (in amperes).
Wire Gauge, Resistance, and Voltage Drop
Note:
AWG: American Wire Gauge (the smaller the AWG number, the thicker the wire).
Diameter (mm): Diameter of the wire (in millimeters).
Copper Ampacity (60°C, 75°C, 90°C): Maximum current-carrying capacity of copper wire at different temperatures (in amperes).
Aluminum Ampacity (60°C, 75°C, 90°C): Maximum current-carrying capacity of aluminum wire at different temperatures (in amperes).
Resistance increases as gauge numbers rise (wire diameter shrinks), reducing efficiency by wasting energy as heat. Voltage drop, the reduction in voltage across the length of a cable, results primarily from resistance. Higher gauge (thinner) cables have increased resistance, causing substantial voltage drops over long cable runs. Significant voltage drops negatively impact equipment performance, causing dimming lights, motor inefficiency, and potential damage to sensitive electronics. Conversely, selecting thicker cables with lower gauge numbers reduces voltage drop substantially, ensuring consistent voltage delivery and optimal device operation.
Key Characteristics of Battery Cables
Battery cables, particularly those connecting energy storage systems to loads or charging equipment have specific features of note:
Large Gauge Diameter: Often ranging from 6 AWG to 4/0 AWG, battery cables carry high current safely.
Low Resistance: Minimizes voltage drop and prevents heat build-up.
Flexible Stranding: Composed of many thin copper strands, battery cables easily bend and maneuver in tight installations.
Durable Insulation: Resistant to heat, abrasion, moisture, oils, acids, and UV radiation, ensuring reliability even under harsh conditions.
These cables primarily supply high-current loads in vehicles, marine applications, solar power storage, industrial machinery, and uninterruptible power supplies (UPS).
Ampacity of Battery Cables
Here is a comprehensive AWG wire gauge vs. ampacity chart for battery cables:
AWG | Diameter (mm) | Max Amps (Short Runs) | Max Amps (Long Runs) | Typical Applications |
---|---|---|---|---|
4/0 | 11.684 | 400 | 250 | ● High-power inverters, heavy-duty truck batteries, marine batteries |
3/0 | 10.404 | 350 | 225 | ● Large automotive applications, industrial battery banks |
2/0 | 9.266 | 300 | 200 | ● High-current battery banks, winches, RV house batteries |
1/0 | 8.252 | 250 | 175 | ● Starter cables, moderate-sized inverter connections |
1 | 7.348 | 200 | 150 | ● Large car audio systems, small inverters |
2 | 6.544 | 150 | 125 | ● Mid-sized car battery cables, smaller power applications |
4 | 5.189 | 100 | 90 | ● Car battery cables, standard automotive applications |
6 | 4.115 | 75 | 60 | ● Smaller RV/solar applications, light automotive |
8 | 3.264 | 50 | 40 | ● Motorcycles, ATVs, small solar setups |
10 | 2.588 | 30 | 25 | ● Small electronics, accessory wiring |
12 | 2.053 | 20 | 15 | ● Low-power applications, signal wiring |
14 | 1.628 | 15 | 10 | ● Very low-power circuits |
Also note:
Max Amps (Short Runs): Maximum recommended amperage for cables used in short-distance applications.
Max Amps (Long Runs): Lower recommended amperage for long-distance runs due to voltage drop.
Voltage Drop Considerations for Battery Cables
Voltage drops can be a big problem in battery cables, especially DC ones carrying high currents. For minimized voltage drops, cable selection factors should include:
Longer distances between batteries necessitate thicker cables.
Higher currents require larger cables.
Pure copper cables significantly reduce voltage drops compared to cheaper alloys or aluminum alternatives.
Designers usually calculate voltage drops via formulas or online tools to decide on the right cable. Under 3% remains a standard industry target for efficiency. For more:
Application | Recommended Voltage Drop Limit |
---|---|
● Starter Cables (Automotive, Marine) | ≤ 0.5 volts (absolute) |
● Solar Power & Battery Storage Systems | ≤ 2% of total system voltage |
● Electric Vehicles & Industrial Battery Systems | ≤ 3% of total system voltage |
● Residential Lighting Circuits | ≤ 3% of total system voltage |
● Commercial Building Wiring (general) | ≤ 3% of total system voltage |
● Sensitive Electronics (Computers, Servers) | ≤ 1.5–2% of total system voltage |
● HVAC Equipment | ≤ 2–3% of total system voltage |
● Industrial Motors & Machinery | ≤ 3% of total system voltage |
● Communication Equipment (Telecom/Data Centers) | ≤ 1–2% of total system voltage |
Voltage drops can be a big problem in battery cables, especially DC ones carrying high currents. For minimized voltage drops, cable selection factors should include:
Longer distances between batteries necessitate thicker cables.
Higher currents require larger cables.
Pure copper cables significantly reduce voltage drops compared to cheaper alloys or aluminum alternatives.
Designers usually calculate voltage drops via formulas or online tools to decide on the right cable. Under 3% remains a standard industry target for efficiency. For more:
Choose the Right Battery Cables for Different Applications
Take into account the specific variables related to the application when choosing a battery cable. Check out the guidelines as follows:
Automotive Systems: Typically use cables ranging between 4 AWG and 1/0 AWG for starter motors, alternators, and battery connections.
Marine Systems: Due to prolonged exposure to moisture and harsh environments, marine applications usually require thick, heavily insulated cables from 2 AWG to 4/0 AWG.
Solar Energy Storage: Solar battery banks typically utilize cables from 2 AWG to 4/0 AWG to reduce voltage drop, especially in remote locations.
Heavy Machinery: Industrial applications and heavy-duty equipment employ heavy-gauge cables (typically 1/0 AWG to 4/0 AWG) to manage high current demands safely and efficiently.
Summary
Wire gauge determines the ampacity or current-carrying capacity; thicker cables (lower AWG numbers) carry more current safely.
Selecting the right cable gauge minimizes voltage drop, ensuring optimal performance, safety, and longevity of electrical components.
Ampacity varies based on
, ambient temperature, heat dissipation, and cable bundling, requiring careful consideration and potential derating in hot or confined conditions.Maintaining specific voltage drop limits—such as ≤0.5 volts for starter cables and ≤3% for electric vehicles and industrial batteries—is essential for reliable electrical performance.
Choosing the appropriate battery cable gauge depends on application specifics like distance, current demands, cable quality, and environmental conditions (e.g., automotive, marine, solar systems, industrial machinery).
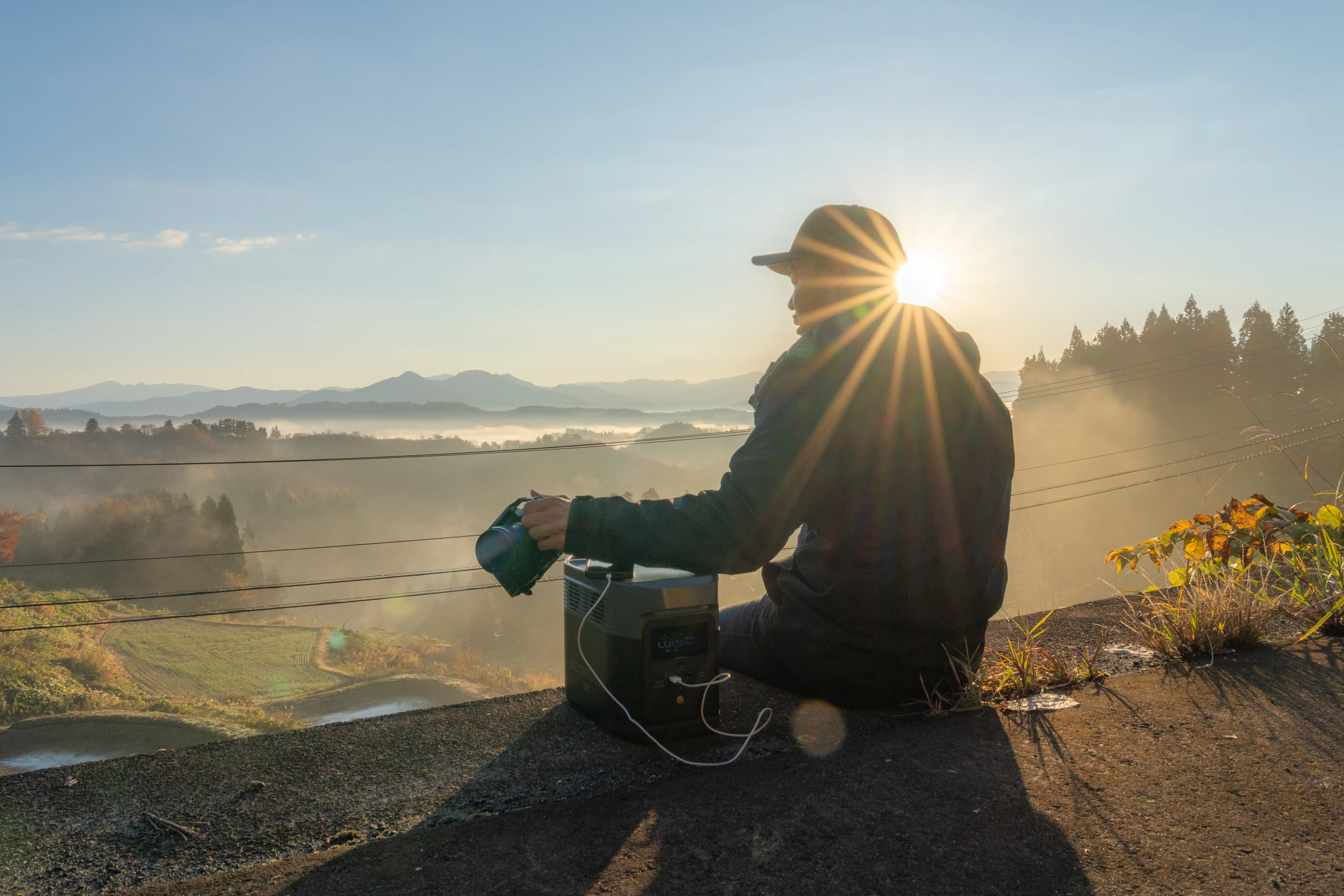